Initially, the Aengenvoort family intended to spend a few days connecting with principals. However, the dynamic atmosphere and a whirlwind of business meetings with print machine manufacturers and suppliers as well as potential customers quickly changed their plans. The Aengenvoorts found themselves making urgent calls to Lufthansa and their hotel in Aachen to extend their stay to capitalise on the unexpected surge of opportunities that drupa presented. Their extended visit became a testament to the event’s vibrant and productive environment, proving invaluable for ROTOCON’s growth and networking ambitions.
PPM editor Anton Pretorius accompanied ROTOCON on a tour of its principals’ stands, which were alive with energy. An unmistakable respect for the team’s success in South Africa was reflected in the warm welcome and admiration from every principal’s representative. The sheer magnitude of advancements on display was awe-inspiring, underscoring ROTOCON’s pivotal role in the industry.
According to André Klinkow, ROTOCON Europe sales manager, this year’s drupa has been one of the most successful shows for the company in recent memory. ‘We were completely overwhelmed by the positive feedback we received, not only from our principals, but also from customers who purchased our equipment at the show. More and more customers are starting to embrace the ROTOCON brand,’ he comments.
During drupa, ROTOCON sold an eight-colour ROTOCON RFP 340 printing press with full LED and a double die station to a label converter in Stellenbosch. The Aengenvoorts also sold two printing presses (one CHROME RFP 450 10-colour and one CHROME RFP 340 eight-colour press with semi-rotary high-speed die cutter) to FLEXOPACK, a label converter in Armenia. Furthermore, ROTOCON sold a RDF 520 to Ren-Flex in Johannesburg. This digital finishing machine is equipped for in-mould labelling (IML) and comes with full- and semi-rotary die cut moulds as well as a special vacuum table, conveyer and anti-static bar to handle IML material.
‘We managed to close some serious deals at drupa,’ Pascal enthuses. ‘On top of that, we received several other enquiries and leads that we’re following up on.’ He adds that ROTOCON has been getting some serious traction on an international level. ‘When a German label printer – a notoriously difficult market for outsiders – is using ROTOCON machines, you know that the technology has been tried and tested,’ he quips.
ROTOCON stands apart from other representing agencies in South Africa by being more than a mere intermediary between manufacturers and customers. It meticulously selects its principals based on quality and alignment with ROTOCON’s core values of excellence, ethical business practices and a sterling reputation. Offering a holistic turnkey experience, ROTOCON provides continuous consultation and advisory services tailored to meet and exceed customer requirements. Its extensive technical and after-sales support, available 24/7, ensures that customers receive excellent service and expertise at every step of their journey. Here are the highlights from ROTOCON’s drupa 2024 tour:
Anytron: any time, anywhere
ROTOCON introduced us to its latest principal, Korean-based Anytron. Isaac Kim, director of the overseas operation department, unveiled Anytron’s latest innovation, the ANY-JET II Plus. ‘This advanced version of our popular inline digital label press is designed to meet customers’ evolving needs, providing a comprehensive solution for fast, accurate and efficient label production,’ Isaac enthused.
We also explored Anytron’s flagship ANY-PRESS, an 13-inch all-in-one digital printer designed for labels and flexible packaging. This versatile printer supports kraft and clear media with white colour support, making it an economical yet powerful option for various printing needs.
In addition to the ANY-JET II Plus, Anytron showcased new applications for its inkjet and LED toner printers, aiming to help brand owners stand out in a competitive market. ‘Our advancements in printing technology offer reliable and versatile options for all label printing needs,’ Isaac noted.
Brotech: a labelling friend

With headquarters in Shenzhen, China, a newly established, state-of-the-art modern manufacturing facility in Xi’an and subsidiary offices and showrooms in Singapore, Germany, the US, Mexico and Thailand, Brotech is making waves as a finishing equipment manufacturer.
Brotech Digital Graphics provides full range label converting and finishing solutions, including hybrid digital and finishing technologies. In addition to regular pressure-sensitive labels, Brotech machinery lines cover IML label, shrink sleeve, cut and stack and booklet labels, EAS, RFID, tickets and tags and many more.
Taking pride of place at the Brotech stand was the new SDF Plus 370, which employs a brand-new modular and platform-based design, enabling it to easily switch workflow directions based on requirements. According to managing director Ramon Lee, whether it’s from left to right or right to left, it can handle both with ease.
CHROME in action


At the ROTOCON stand, the company demonstrated the CHROME RFP 340 in action – a model that André Klinkow, sales manager for ROTOCON Europe, recently sold to German label printer Dialogic. The eight-colour CHROME RFP 340, featuring an upgraded servo motor, provides label and flexible packaging printers with enhanced customisability and modular upgrade options to expand their market reach.
According to Pascal, this cost-efficient flexographic printing press balances registration accuracy with high running speeds. The RFP – an eight-colour press with a die-cutting station – uses the latest Bosch Rexroth double servo drive and control system on the print drive. Each printing unit has double servo motors, one for the sleeve cylinder and the other for the impression roller (which is also a cooler roller).
ROTOCON recently partnered with UV curing systems technologist Height-LED to enhance the ECOLINE CHROME RFP. Established in 2011, Height-LED produces low-maintenance, energy-saving and cost-efficient UV curing lamps. ‘These LED and UV systems offer the highest curing intensities available for printing, thanks to patented technologies that are years ahead of competitors’ designs,’ commented sales manager Cheng Mandi.
Erhardt + Leimer: a vision for the future
The next stop was vision inspection system principal Erhardt + Leimer (E+L), where product manager of inspection technology Alexander Thomalla explained that the term ‘200% reliability’ on the SMARTSCAN is not a marketing gimmick thanks to a unique double image acquisition method for inspection. Here, two image streams are acquired with a temporal offset – once with incident light and in parallel with transmitted light (hence the 200%). The advantage is that, along with classic print defects, material defects such as damage in the label or on the carrier, unremoved matrix, offset on the cutting position, splice points or residue on the rear of the label become visible.

EyeC: seeing is believing
ROTOCON and PPM also experienced EyeC’s innovative and fully automated systems firsthand, including the EyeC ProofRunner Carton HighLight and Proofiler 1200 DT. EyeC service technician Sascha Nather and business development director Ralph Beier discussed EyeC’s intelligent AI algorithm, which compensates for typical printing process fluctuations and displays only relevant deviations. The intuitive user interface allows for a complete, reliable and documented inspection in just a few clicks, delivering precise results.

Pantec: precision in embellishment
At specialist embellishment equipment manufacturer Pantec’s stand, we witnessed its rotary hot foil embellishment technology (CHEETAH) and foil embossing system (RHINO) in action. These systems enable the narrow-, mid- and wide-web industry to add any metallised or haptic effect, from foil embossing to nano embossing, helping products win the battle on the shelf.
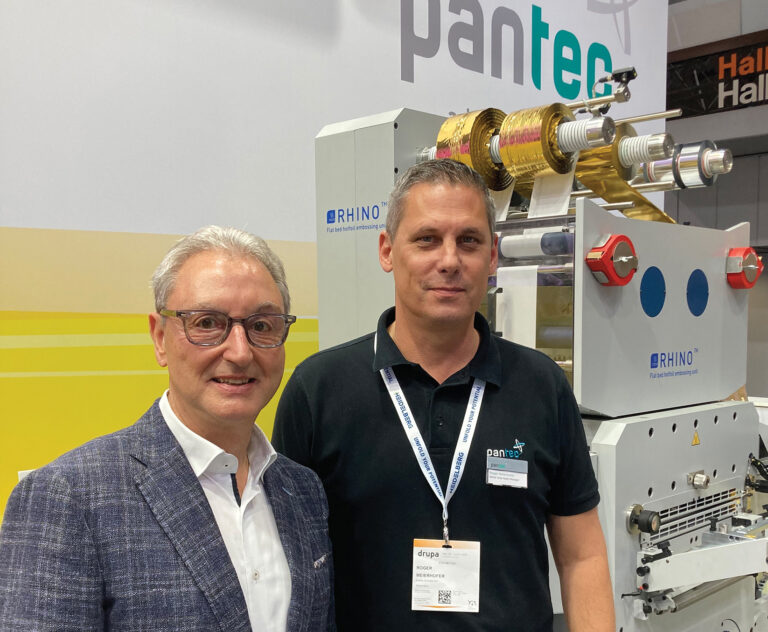
EMT: taking (Roto)control
On day six, we dropped by the stand of Rotocontrol/EMT International. Here, EMT demonstrated its modular Chameleon finishing line, including unwinding, the DP22 PRO dynamic perf and punch continuous feed processor and the RFX cut-stack solution. This finishing line supports digital printing applications and press materials with high-speed performance and enhanced flexibility, handling up to 10 processes in one machine.

SCREEN: a sustainable innovation
ROTOCON also introduced PPM to SCREEN’s latest innovation, the Truepress PAC 520P. This high-speed, water-based inkjet digital printing system, which marks a new era in paper packaging, is now available in South Africa.
According to Steve Low, SCREEN’s vice-president of service and support, the flexible packaging industry faces increasing pressure to reduce its environmental impact. ‘One rapidly growing trend is the reduction of plastic material used in packaging,’ he remarked. Studies show that consumers prefer paper-based packaging, perceiving it as more environmentally friendly and easier to recycle. In response, SCREEN has launched the Truepress PAC 520P, which uses proprietary water-based pigment inks that comply with food safety regulations, offering a much lower environmental impact than conventional printing processes alongside outstanding print quality and safety while maintaining exceptional throughput, Steve added.
drupa 24 highlighted ROTOCON’s strong partnerships and commitment to supporting its principals, driving forward a future of efficiency, precision and environmental responsibility in the printing world.
