Müller Martini’s Vareo perfect binder was originally launched at Hunkeler Innovationdays 2015 in Lucerne, Switzerland. ‘We struck a chord with our customers with this perfect binder, which was predestined for digital and offset printing and has a capacity of 1 350 cycles/hour,’ says Ronald Reddmann, product manager of Perfect Binding Systems. For the first time, each of the three grippers on a perfect binder was equipped with its own servo motor and driven individually, allowing each processing step to be individually adapted to the product.’
‘In 2019, Müller Martini updated the Vareo with features that optimise production. The new 18½-inch touchscreen with clearly structured menu navigation including animation of corrections allows operators to see all important production parameters at a glance and thus have quick access to all stations. The intuitive user interface allows short changeover and production times.
Fully automatic edge banding
‘We have completely redesigned the hot melt spine gluing system for ideal glue flow and temperature control,’ he adds. It is equipped with two applicator rollers and a separately heated counter-rotating spinner roller. The two roller systems can now be adjusted in height independently of each other. Edge gluing is now fully automatic as standard, which means that all settings are reproducible.
Nozzle and adhesive application control systems
To ensure adhesive loss-free glue application with monitoring for top quality, particularly in the ultra-short-run and book-of-one areas, Müller Martini developed a new PUR nozzle system for the Vareo PRO and adhesive application control system.
‘The PUR nozzle system with volumetric circulation system guarantees perfect glue application and reliable binding with a wide variety of materials,’ says Ronald. ‘A fully variable nozzle head ensures perfect and loss-free spine glue application from book to book. Operators can clean and maintain the PUR nozzle system quickly and easily. This means they can increase productivity by up to 20%.
The laser/camera-supported monitoring system, which is equipped with new algorithms for even more precise glue application. Both quantitative (glue present or not) and qualitative (glue layer thickness, edge gluing) monitoring are carried out in 2D and 3D display on the touchscreen.

Modular design
The Vareo PRO has a modular design so that print service providers can easily expand the machine, into a complete perfect binding line, for example, with a customer-specific cooling section, a three-knife trimmer or an automatic book block feeder. This enables the Vareo PRO to be connected to digital presses. The finished signature or loose-leaf piles are then transferred directly to the perfect binder’s gripper.
‘A particular advantage of the Vareo PRO is its optional book thickness measuring device. It allows efficient single-book production – without any waste,’ he reports. ‘The optional format measuring station can be used to measure book block formats, cover formats and creasing positions, and the entries are automatically transferred to the control system.’
Effective spine processing
The milling tool combines dust milling, roughening, notching and brushing and can process book thicknesses of up to 60mm. The milling depth is entered automatically on the touchscreen. Even digitally printed loose-leaf piles are reliably and stably guided. For thread-sewn or thread-sealed products, operators can lower the milling station as standard.
Specially for digital print shops, an encapsulated milling dust extraction system is also available, which is adapted to the room air requirements of digital printing presses.
Barcode recognition avoids waste
‘To ensure that contents and cover match correctly, print service providers can equip the Vareo PRO with integrated barcode recognition,’ says Ronald. The cover barcode is measured before creasing. This means that an incorrectly inserted cover does not result in waste but can be reused. Especially for hardcover finishing, an integrated inkjet printer can apply an additional barcode to the bound book block, which can be compared with the book cover during subsequent insertion.
Trim options
The Vareo PRO (in line with Müller Martini’s Finishing 4.0 philosophy and especially for very short runs) is at its best when used with the InfiniTrim three-knife trimmer. This trims short and very short runs with all book formats and thicknesses automatically.
For medium runs, a combination with the Granit three-knife trimmer is also suitable as SmartPress technology enables cost-effective production in a variety of applications.
‘Additionally, each Vareo PRO line can be expanded into a cell. For example, Müller Martini has successfully installed extensions with up to four Vareo PROs into one InfiniTrim. Extensions in the direction of hardcover book block production are also possible without problems. If later expansion requirements are known, this can already be taken into account during the layout creation in the first phase,’ Ronald explains.
All-rounder for offset and digital printing
‘The all-rounder Vareo PRO with its excellent price/performance ratio shows its strength not only in digital printing with very short runs down to the book of one, but also in medium runs – regardless of whether production is in offset or digital printing. This makes the Vareo PRO the ideal binder for bookbinders and printers who work with conventional printing processes and are planning to move into digital printing or are already active in digital printing,’ he concludes.
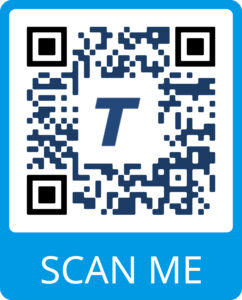
Scan the QR code for a demo video of the Vareo Pro.
Ed’s note: Müller Martini’s Vareo PRO perfect binder is available in southern Africa from Thunderbolt Solutions.