The Onyx Go offers the fastest printing speed in the short-run flexo segment at up to 400m/min, which enables converters to print up to 50 million square metres annually across three print widths: 820, 1 020 or 1 320mm.
It also provides the fastest changeovers in the ultra-short and short-run flexo segment at under three minutes to set up printing pressures and register, enabling converters to gain up to 240 extra hours of production/year compared to competitor solutions.
Active Pack allows converters to equip their Onyx Go presses with top-notch sustainability technologies. Active Pack consists of three components: Active Start, Active Ink and Active Dry. This package can save converters more than €100 000 annually on energy and material consumption and actively helps them to repay the machine in a shorter time.
This is thanks to the Active Start feature that automatically recognises printing plates and sets the printing pressure and register. The system recognises the cliché’s 3D characteristics and transmits the printing set-up information to other machine components such as the drying and inking systems and ensures repeatability across different jobs.
Active Start, also, automatically adjusts the printing pressure among the cylinder, cliché and substrate almost instantaneously, enabling repeatable performances over time.
Sustainable
The automatic printing pressure and instantaneous register setting system make it possible to minimise material waste to 18m during the set-up phase of each print run. Additionally, the patented Active Dry® system (part of the Active Pack package) optimises energy consumption by regulating the drying power according to the printing characteristics. It is assisted by the ventilation system, which guarantees perfect insulation and saves up to 50% of annual energy consumption versus comparable flexo presses without this patented Smart Drying system.
It is complemented by the Active Ink dosing system (part of the Active Pack package), which has been positioned on the side of the CI drum to optimise the ink flowing into the circuits. This dosing system detects the printing characteristics on the cliché, optimises the quantity of ink pumped to each printing unit and saves up to 60% on annual energy consumption compared to other flexo presses without the Active Ink system.
The Sprint Wash system saves up to 40% of solvent consumption annually versus comparable flexo presses on the market because it completes washing cycles in less than three minutes and enables constant washing performance on all the printing units, regardless of their position.
The Dynamic Ink (Dynamic Doctoring) system automatically regulates ink flow by means of dynamic dumpers placed on the sides of the doctor blade, which open/close and optimise inking system pressures for greatest printing quality. Uteco’s R&D team has also chosen an extremely light doctor blade (less than 10kg) to reduce blade wear and consumption.
Compact
With a total footprint of 50m2, the Onyx Go has been designed to minimise the off-press operating space and free operational space on the back of the machine.
Easy and safe to operate
Uteco’s engineers have strived to create a noiseless design by selecting materials to reduce vibration and noise levels to below 80db. Operators can regulate ergonomics through the Dynamic/Adaptive Cockpit by adjusting the level of the high-tech HMI according to their height and maximising its automated features, which are connected with external systems for real-time data monitoring and processing.
Operators can also easily remove the upgradable Dynamic Drying Box (toolless) with a single move to directly access the central drum when cleaning and maintenance are required. Furthermore, they can easily replace the drying box nozzles with different shapes to enhance the drying power when required.
Operators no longer need extra equipment or ladders to reach and change higher colour units, thanks to the two Dynamic Lifts that have been integrated within the CI Unit and positioned in correspondence with the first and last colour units.
It is now easier and safer for operators to substitute the splice guards for washing and maintenance purposes because they don’t need tools – the Sprint magnetic system allows them to simply attach and detach these guards.
Operators can easily access the upper part of the machine by means of a catwalk that extends to the total length of the press and a fixed ladder positioned on the rewinder rear side. This design makes it easier for them to safely monitor the web and easily access the CI drum and the drying system for cleaning and maintenance.
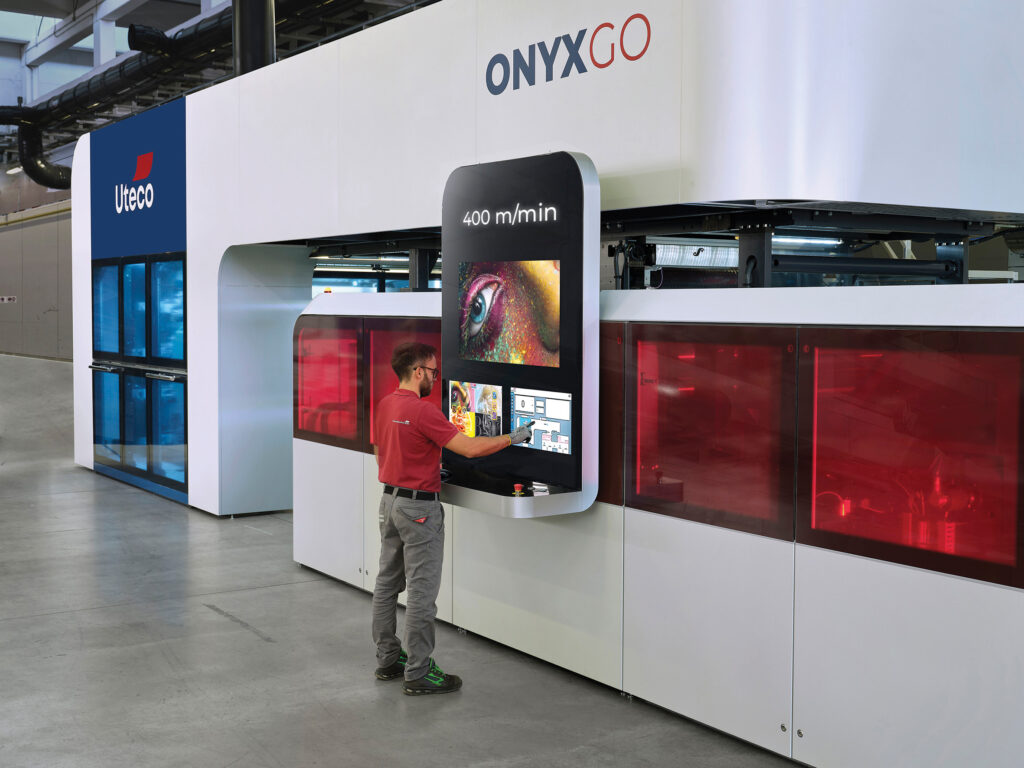
Versatile
The Onyx Go has been designed as a multi-ink (water- and solvent-based), multi-material (plastic films, aluminium, paper, cardboard and laminates) and multi-industry (food and beverages, pharmaceutical, health care, personal care home, office and industrial) CI flexo press.
Converters can boost the Onyx Go’s end-use application flexibility even further by ordering a Uteco kit configuration best suited to their needs.
1. Water-based KIT: These printing inks demand special requirements, for example, stainless steel, pH control and anti-foam.
2. Heavy Duties KIT: Provides the proper management of heavy materials such as cardboard or paper, which require special tensioning and web threading mechanisms.
3. Tropicalisation KIT: Production sites located in warm climates need extra care on the cooling systems and treatment of substrates, especially if the latter are very extensible.
4. Aluminium KIT: For production environments using aluminium substrates.
Uteco is represented in southern Africa by Sareltech. Visit www.sareltech.com for more information or email: marketing@sareltech.com