According to Corné Pretorius, GM of Nissei ASB South Africa, Zero Cooling technology takes full advantage of ASB’s proprietary four-station, one-step moulding method, by shifting virtually all preform cooling away from the injection station and into the second, conditioning station, dramatically reducing injection cycle times.
Crucially, the Zero Cooling moulding method facilitates short cycle times while removing the need for thin-wall preforms that are susceptible to quality-related problems, most notably undesirable ‘fisheye’, ‘body ring’ and ‘orange peel’ effects.
In Corné’s opinion, the second-generation ASB-12M expands production capabilities for a vast range of PET containers, including lightweight bottles and wide-mouthed jars, attaining the highest quality at low capital investment.
The model demonstrated at K 2019 was using a four-cavity mould to produce 46ml and 80ml glass-like cosmetics containers in a cycle time of 12.5 seconds. It was also fitted with an optional IU-10L long-stroke injection unit, illustrating the 50% increase in available shot-size to expand the scope for large containers, heavyweight cosmetics bottles, or lower-density materials such as polypropylene.
The fourth-generation ASB-70DPH combines the ability of moulding PET and up to 20 other resin types with the versatility of producing bottles below 100ml using up to 12-cavity moulds through to 10-litre capacity jars using a single cavity.
At the show, it was moulding a 250ml cylindrical shampoo/cosmetics container (with 10 cavities) at a cycle time of 12.9 seconds to produce more than 2 600 bottles/hour.
The Advanced Version of the ASB-70DPH, using an eight-cavity mould, was producing 30ml, 19mm screw neck containers for medical or toiletry products in a cycle time of 4.4 seconds, generating more than 6 500 bottles/hour.
In addition to the reduced cycle time offered by Zero Cooling technology, the machine provides a 40% reduction in indexing time, enabling the container (with a short preform) to be moulded up to 2.4 seconds faster than a standard model.
As Corné points out, the demonstrated container design falls into a category that’s often difficult to mould with perfect visual quality. ‘Its small neck-to-body diameter ratio and higher-than-normal weight, meeting customers’ requirements for “quality feel” products, would cause moulding compromises with a standard mould,’ he maintains. ‘However, Zero Cooling technology creates a two-fold benefit: it helps to improve productivity and ensures flawless visual quality of the container.’
Nissei describes the ASB-70DPW as the versatile double-row moulding equivalent of the ASB-70DPH. It’s optimised for the production of smaller bottles in moulding configurations from eight to 24 cavities, and containers up to one-litre capacity.
It’s now fitted with an enhanced mould-changing system in all stations that reduces blow mould changeover times by 70% and complete preform and blow mould changeover times by around 50% compared to previous-generation designs.
At K 2019, the ASB-70DPW was moulding an oval 100% rPET shampoo bottle (300ml) in 14 cavities at a cycle time of 13.38 seconds, generating more than 3 700 bottles/hour.
Each of the five machines were displayed with a full line of matching moulding ancillary equipment such as resin dryers, chillers, dehumidifiers, etc.
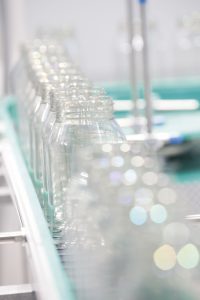
Showing off the capabilities of the ASB-150DPW, a 900ml, 70mm neck general food jar was being moulded using 100% rPET. The machine’s Zero Cooling technology enabled a cycle time of 8.97 seconds and a productivity rate above 5 300 jars/hour.