‘The third-generation Jet Press 750S complements the division’s conventional offset presses (turn to page xx for details) with its versatile variable data capabilities and offers a more cost-effective way of printing short- to medium-runs (from one to 1 000), as well as bi-election and local election materials that run at much smaller volumes than national election ballots,’ states CEO Keith Michael.
Keith points out that the new dispensation for municipalities to do audits on buildings for evaluations is resulting in an uptake of variable data printing for bills. ‘Print service providers (PSPs) will need to prove that they can manage and execute data files and print updated files. Printing is the easy part, while managing the data is trickier,’ he maintains. ‘However, over the years, through all our work with various government departments and corporate organisations, and the digital capabilities created by the Lebone Media team, we’ve built a strong data set/bank and know how to safely manage large data sets.’
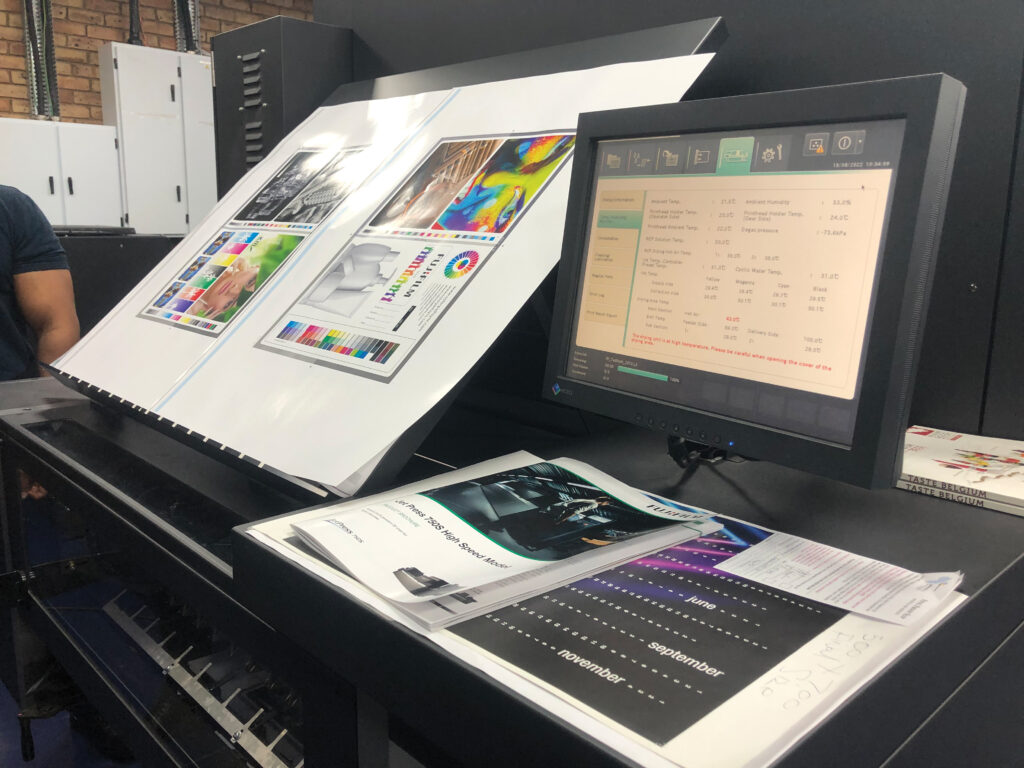
Double-sided variable data handling
Gary Stockenstroom, Fujifilm Graphic Systems South Africa’s digital product manager, maintains that the Jet Press 750S is currently the fastest B2 digital sheet-fed press on the market (at 5 400 sheets/hour), offering beyond offset quality (at 1 200 x 1 200dpi and 30-billion droplets/second) and the capability to run the same paper stocks as offset presses.
Gary explains that the Jet Press 750S’s ultra-high capacity data servers transmit variable data alongside printed output, facilitating efficient variable data production at the full press speed of 5 400 sheets/hour.
The press also utilises a barcode system to guarantee front- and back-page matching. The barcode is printed in the non-image area of every sheet immediately after the paper leaves the input sheet stacker. Once the first side has been printed, the sheets are turned over and reloaded into the sheet stacker. The press then reads the barcode on each sheet as it leaves the stacker and downloads the correct page information before it prints the second side, guaranteeing front- and back-page matching. ‘The benefits of this capability extend beyond the obvious application of variable data personalisation. Jobs can also be printed collated in page order to simplify and speed up the finishing process or improve the logistics for job distribution, making the production of versioned print jobs simple,’ Gary enthuses.
Blended approach optimises reliability, versatility and carbon footprint
Keith also appreciates that the Jet Press 750S blends the best of old and new technologies. The Jet Press 750S is built on an offset chassis and features a traditional sheet-fed paper feed mechanism, which adjusts automatically when the paper size is selected and ensures high registration accuracy from sheet to sheet and reliable operation. ‘This press enables us to take advantage of our current paper stocks because we can use standard coated and uncoated offset paper, rather than specialised coated digital paper, which simplifies inventory and reduces costs. Additionally, it enhances our team’s ability to take advantage of diverse paper types and effects in the future and increases the press’s versatility.’
Gary points out that the digital inkjet printing technology eliminates the preparation and set-up time of an offset press – there are no plates to produce, no platesetters or processors to maintain, no make-readies, no run up to colour, no waste sheets and only three pressroom consumables. Combined, these factors help improve the environmental performance of the Jet Press 750S.
He lists the other digital technology benefits as the latest 1 200 x 1 200dpi Dimatix Samba inkjet printhead technology, Rapid Coagulation Primer to counter dot gain, an In-Line Sensor system that detects nozzle and ink deposition inconsistencies, a new drying system for faster job turnaround times plus a 23% reduction in power consumption from 428A to 330A compared to the Jet Press 720S and enhanced colour gamut.
Gary explains that Fujifilm’s development team has increased the printhead jetting frequency from 25 to 33kHz to speed up dot placement and counteract the increased effects of possible turbulence. ‘The primer unit applies a clear and odourless ultra-thin film Rapid Coagulation Primer (RCP) onto the paper via an anilox roller mechanism to counter the natural tendency of the ink droplets to spread when they hit the paper and create dot gain. The RCP also prevents the ink pigments from sinking into the structure of the paper, making them easier to remove during the deinking and recycling process,’ he reports. ‘Additionally, print quality is improved via the proprietary In-Line Sensor system, which scans every sheet and detects any nozzle and ink deposition inconsistencies, modifying the printhead nozzle map and ink deposition parameters in real-time to correct deviations from the norm.’
The new drying system features a transport belt, heated via rollers from above, with a vacuum applied to each sheet as it passes through this section to ensure uniform heat application and sheet stability. The sheets then pass under a bank of cooling fans, designed to optimise their temperature and ink drying performance, before they are delivered to the sheet stacking tray.
According to Gary, the Jet Press 750S’s enhanced colour gamut called MaxGamut allows PSPs to reproduce more spot colours and more vibrant print with just four CMYK inks, without having to add or swap special inks or toners to boost the colour.
‘The MaxGamut’s primary advantage is its ability to accurately reproduce 90% of the Pantone colour library within a specific Delta E variance of three or less, he notes. ‘PSPs can use the XMF ColorPath Brand Colour Optimiser module as a quality control tool to see how accurately a Pantone colour will be printed on a specific media type.’
He asserts that B2 digital inkjet represents the perfect tailored technology for forward-thinking commercial PSPs to adapt their businesses to changing market conditions, where high-quality, value-driven, short-run jobs are becoming the norm and turnaround times are reducing from days to hours. ‘PSPs investing in the Fujifilm Jet Press 750S can be more productive, take on more work and get more sheets on the floor than with multiple digital presses. This is thanks to the press’s maximum production rate of 5 400 sheets/hour, 90% uptime because there are no pre-press plates or chemistry, no make-readies and minimal waste as the first printed sheet is saleable.’
Gary adds that beyond secure printing applications, the Jet Press 750S B2 sheet-fed digital press prints on cartonboard, photo canvas and some plastic materials to produce short-run coffee table books, photobooks, brochures, personalised calendars, art posters, single-sided book jackets or versioned short-run packaging material to coincide with specific events or store promotions. ‘Modifications to accommodate heavier weight folding carton stock from 0.2 to 0.6mm in thickness are possible. The press can be supplied with low-migration, aqueous food-safe inks that comply with international regulations for primary food contact packaging applications,’ he concludes.
Inspiring next-generation skills
IN keeping with the Fujifilm Jet Press 750S launch theme of The future of print is digital and to showcase the opportunities that digital platforms are opening for women alongside traditional technologies within the industry, Lebone Litho Printers invited 30 female learners from Jordao College in Turffontein to the event.
In addition to seeing this first-of-its-kind press in action in Africa, the learners were guided on a two-hour tour by CEO Keith Michael through the rest of the Lebone Print Secure division, the commercial and packaging printing divisions, as well as the platemaking and graphic design departments, to gain insights into the equipment, materials and processes the company uses plus the variety of products it produces.
‘Skills shortages within our industry are very evident and we need to raise awareness among learners about the career options and bursary opportunities available to them within the printing value chain,’ Keith explains. ‘Our team is also passionate about education and entrepreneurship, and encourages opportunities to support, motivate and inspire learners in nearby communities.’
Click here to read this article in the E-Mag.