The BST Group, locally represented by Sareltech since 2008, has recently replaced its trusty Super Handy Scan 4100 with the modular and customisable PROView video web monitoring system to provide real-time print image monitoring at printing speeds beyond 1 000m/min across narrow and wider material webs, thanks to the traverse mounting. According to the development team, their focus was on versatility and design simplicity, from commissioning via plug-and-play through to intuitive operation and convenient remote maintenance.
The basic version of the PROView monitoring system offers a range of functions, including a durable lighting unit, position memory, split screen and virtual repeat, which make process flows more efficient.
An LED strobe ensures homogeneous illumination of the material web. UV strobes to make fluorescent pigments visible and lacquer strobes to make coatings visible by changing the angle of illumination can be easily retrofitted via plug-and-play.
The position memory function saves an unlimited number of camera positions – including the settings for field of view, zoom, iris and position along the web length – making them easily retrievable at any time. Additionally, the number of jobs that can be stored is unlimited, depending on the available hard disk space.
On the split screen, the reference and actual image can be displayed at the same time – in line with the saved settings for field of view, zoom, iris and position along the web length – and can be directly compared with one another. This functionality makes it possible for the operator to continually compare the appearance of the current print and a reference sample.
Operators can also navigate the camera across the printed web via the virtual repeat function. With one keystroke, they can create the entire format as a single overview image.
Thanks to its modular design, the PROView system is adaptable to PSPs’ needs. In addition to two camera and lighting units in different sizes, they can choose to add the Snapshot Gallery, Semi-automatic CI Register Control, Haze Guard, Relative Colour Measurement and Front-to-Back Control.
The Snapshot Gallery enables remote monitoring of production via the PSP’s network and can save up to 50 live images per job, while the Haze Guard makes the visualisation of missing lacquer and any type of defect due to weak contrasts, such as colour streaks and scumming, possible.
The Semi-automatic CI Register Control provides fast and specific support for register setting in the event of machine downtime and fully automatic register control on machine start-up. Operators can assign inking units and all other colours to printing units via the monitor.
Relative Colour Measurement helps to identify colour deviations as compared to previously defined colour values. Operators can freely select measuring points and display status defect reports. There is also an optional alarm traffic light to warn them of colour deviations.
Front-to-Back Control is possible with an optional backlight strobe as it enables observation of the front and reverse side of the web. Operators can choose between alternating or simultaneous display (in split-screen mode) of both sides. The backlight strobe also helps to eliminate shadows cast by translucent materials.
Wide-web press and slitter inspection
BST’s TubeScan digital strobe modular inspection system is now available for wide web applications (widths of between 900 and 1 700mm) on printing presses and slitters and can be easily integrated into the QLink production workflow.
TubeScan XL provides excellent image quality for 100% web inspection on the press. It uses advanced matrix camera technology to take and display up to
30 images/second in live mode. Image stabilisation is also assured thanks to automatic format synchronisation across the entire speed range of the press. Combined, these two functions provide seamless monitoring of every repeat in real-time.
Operators can analyse areas in detail, using the high-resolution zoom functions on the 812mm monitor.
Recurring errors from faulty printing plates, for example, can be detected at an early stage to minimise unnecessary costs for misprints and shorten make-ready times. Colour consistency can be ensured via ΔE monitoring.
When integrated into the QLink workflow, TubeScan XL stores the defect data in roll logs. These can be used later for quality assessment or in further production steps to eliminate defective material. The stored production data can also be used as proof for customers.
The stroboscope function of TubeScan XL on the slitter, which accommodates speeds of up to 800m/min, produces a crisp, stable image for monitoring and evaluating print quality. Operators can use the zoom functions on the 812mm monitor to accurately analyse detailed areas.
When automatic print control is activated, TubeScan XL detects sporadic or recurring errors in colour and text areas and stores them in an error log. This can be used for downstream quality assessment and as proof for customers.
During inspection on the slitter, the QLink workflow system records quality data and stores it on a server. Each slitted lane is treated separately and an error log is created on the slitter for each individual daughter roll, making its selection for further processing easy. Relevant daughter roll statistics are concisely displayed on the screen for operators. Based on the defect presets, QLink Slitter categorises the material as defect-free, waste and to be doctored. TubeScan XL controls the bidirectionally operating doctor machine so that the defect is automatically placed at a predefined target position. The doctor machine then uses the QLink protocols to remove the waste, ensuring quality control and maximum yield.
Object-oriented web guiding
The recently introduced CLS CAM 100 sensor uses a colour matrix camera to enable the precise detection of objects, lines, print marks or web marks at web speeds of up to 1 200m/min.
Web guiding based on the print layout offers several advantages compared to traditional guiding criteria like web edge or trimlines. The main advantage is that an extra control line at the edge of material is no longer necessary, which saves up to 2% of total material costs. This, for instance, equates to a three-ton saving when 150 tons of flexible material are used monthly.
Additionally, possible web guiding fluctuations no longer have any influence on the control accuracy since the CLS CAM 100 also allows scanning for objects directly in the centre of the web. The measuring range is 60 x 40mm for control criteria up to 30 x 30mm.
Operators can select the control medium via a swipe gesture on the touchscreen and easily save control criteria, allowing for faster subject changes and precise web guiding results. Furthermore, job installation can be done within three clicks or touches and the automatic job and set-up saving functions help to minimise make-ready times.
Ed’s note: Sareltech supports many key BST Group customers in South Africa with new installations, upgrades, support and local stock of critical components to ensure minimum downtime on their production machines.
Click here to read this article in the E-mag.
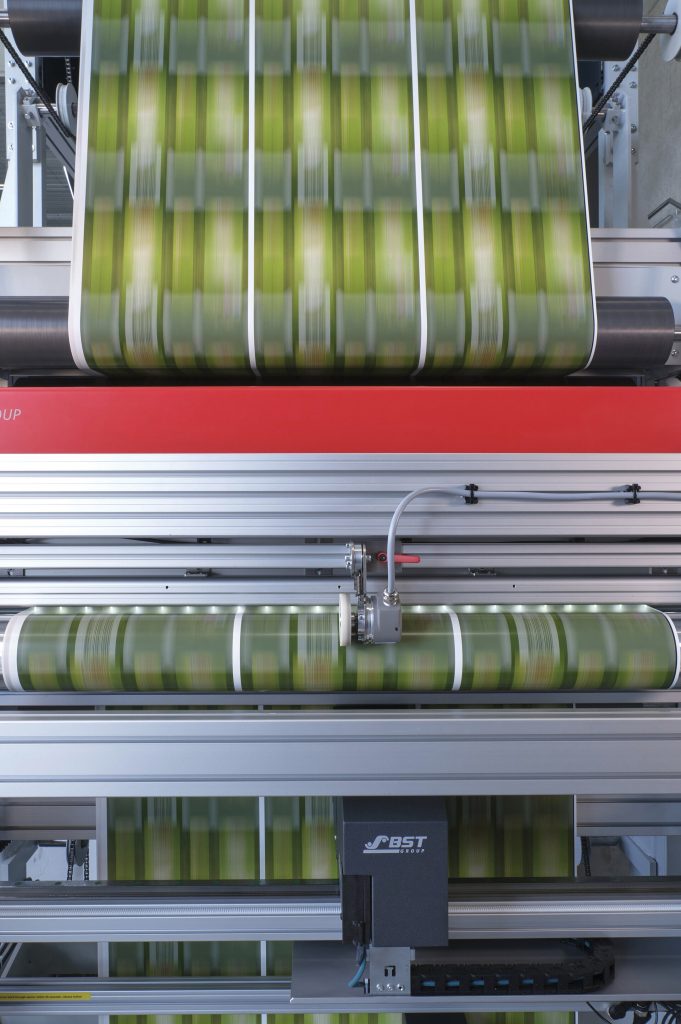